Real-time insights for
optimized mineral processing
Custom-built for high-temperature processes, the Blue Cube High-Temperature Analyzer assists operators by empowering them with real-time insights for improved decision-making. By providing real-time quality data, process control cycles can be significantly improved.
High-temperature measurements are achieved by placing a robust optical probe in a strategic position to view the calcined product as it falls out of the kiln. It projects an incident flashing light beam and collects the reflected spectral data in the ultra-violet, visible and infrared ranges several times per second.
Draslovka’s unique technology provides multiple measurements with a single instrument. State of the-art spectroscopy and mathematical modelling are used to provide these real-time measurements that enable efficient process control, such as percentage overburn, measurement counts, particle sizes and temperatures.
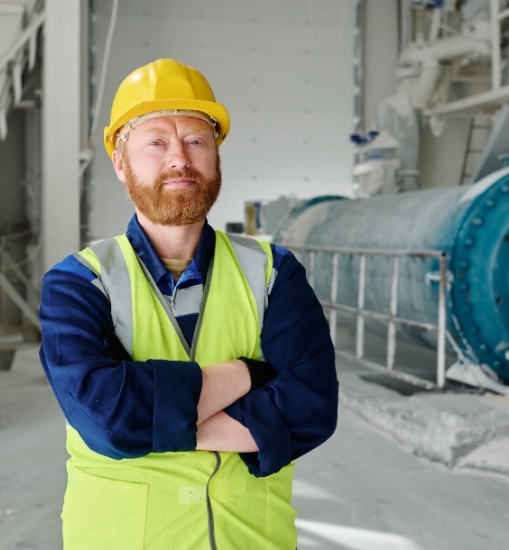
Low maintenance system
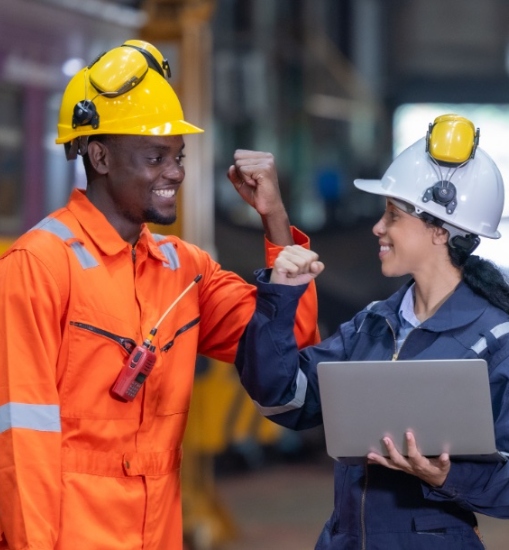
Modular design: Simple installation
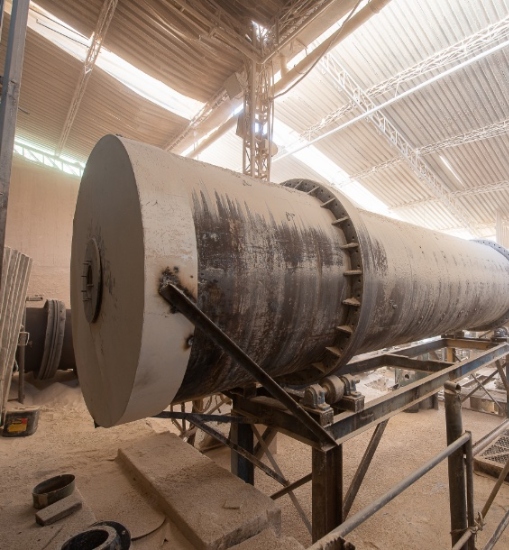
Minimal infrastructure
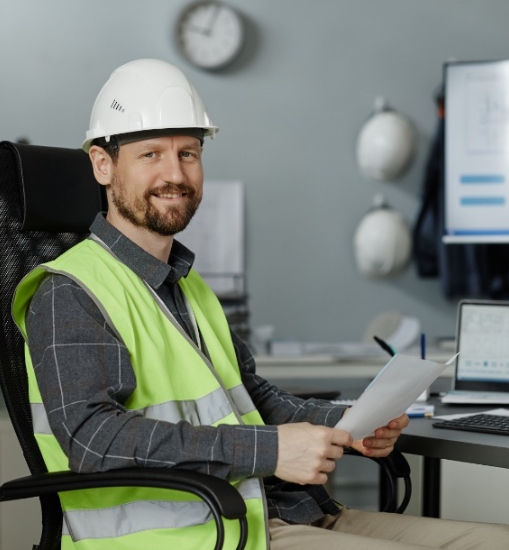
Real-time quality measurements
Typical applications
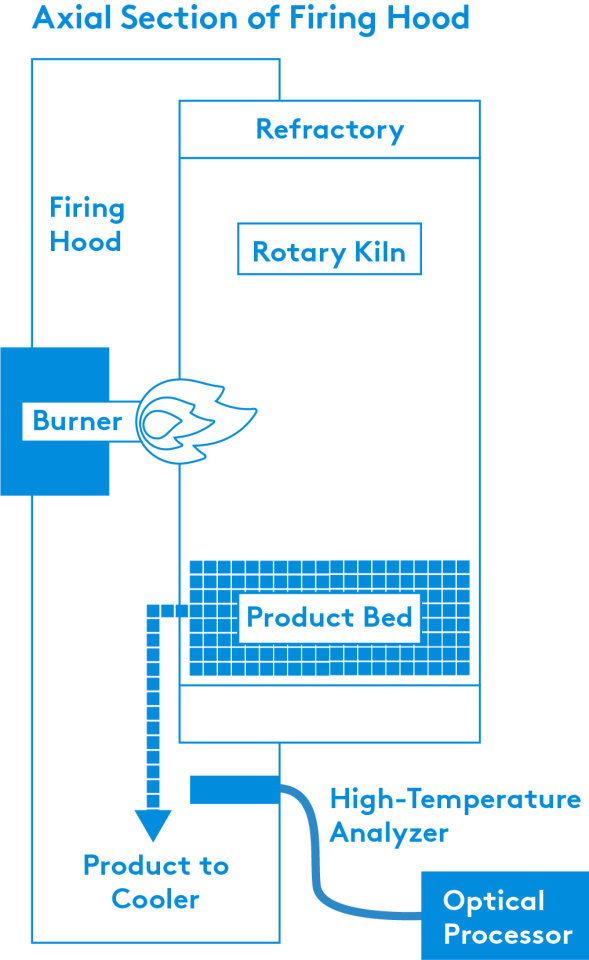
How it works
High-temperature measurements are achieved by placing a robust optical probe in a strategic position to view the calcined product as it falls out of the kiln. It projects an incident flashing light beam and collects the reflected spectral data in the ultra-violet, visible and infrared ranges several times per second.
The spectra obtained are compared to the calibrated signature spectrum of the desired product quality. The deviations are then used to generate statistics of readings above and below the target quality typically expressed as a percentage of the total measurements above or below the target. A selected percentage value may be used as control inputs to the process (for example the firing rate) to achieve the desired product quality consistently in an automated control loop.
The key to the successful operation of the analyzer lies in ensuring the optical processor is able to view the product particles as they fall over the refractory lip, out of the inclined rotating kiln.